Sir Walter Scott said, “It is more than probable that the average man could, with no injury to his health, increase his efficiency fifty percent.”
While that may be true, your people don’t intend to be inefficient; they just do what comes naturally in the work environment YOU provide. If they have to jump over hurdles, most won’t complain, but you’ll pay extra for each jump. Let me explain.
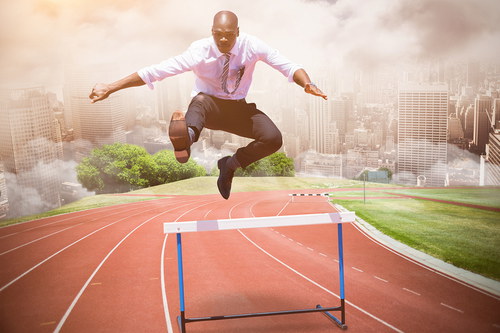
In every business system or process, there is the potential for “system busters,” “speed bumps,” or “time traps” that drag down system performance, add to human error, reduce quality, and increase labor costs. You need to put on your System Thinker’s hat, identify these termites that are eating away profit, and exterminate them.
Below are eight such system busters to look for:
- Physical impediments create a waste of time and effort (e.g., an obstructed aisle; clutter; things hard to find; piles; messes; unsafe or uncomfortable work conditions; general disorganization).
- Extra movement from a poor layout of work areas and walking distance adds time to complete a task. When this is multiplied by many people over the course of a year, it can be very costly (e.g., printer at the far end of an office; poorly laid-out production area or warehouse; unnecessary steps in a process).
- Distractions are small interruptions that cause people to lose focus on the task at hand. Continuity and momentum are disrupted. These can be big time-wasters and the source of mistakes (e.g., workers look up to see people coming and going; personal telephone calls; excessive talking with co-workers; surfing the Internet).
- Mistakes and rework require a duplication of effort and lost time that could be spent more productively (e.g., handling rejects on an assembly line; processing returned merchandise; researching data entry errors; returning to a job site to fix a problem).
- Downtime is a major interruption to system flow. A system or process stops because another system is dependent upon breaks down (e.g., needed supplies don’t arrive on time; power outage; corrupted or lost computer file; work stalled at a bottleneck). Every in-basket or pallet of materials waiting to be worked on is in a state of downtime!
- Start-stop workflow occurs when people work more than one system or process (job function) and switch between them. This decreases concentration and momentum, increases the risk of operator error, and makes it difficult to measure performance (e.g., shifting production schedules; “multitasking,” “wearing multiple hats,” or being “spread too thin”).
- Complexity, incompetence, or confusion can make it difficult for people to follow through on instruction or direction given (e.g., poor documentation; inadequate training; multiple bosses; conflicting priorities; too many choices/options). Keep it Simple!
- Unfinished items are a mental and emotional drain, and decrease efficiency (e.g., back-orders, accumulation of tasks, half-finished projects; long to-do lists). The more incomplete items there, the longer the completion time stretches out for each of them. Stay focused on a few things and be a finisher!
Wasted Time is Never Recovered
You can’t eliminate all the speed bumps, time traps, and system busters. However, with the eye of a Systems Thinker, you can cut a lot of wasted time from your operation.
Fix your faulty systems or processes before trying to fix people. The cause of inefficiency is usually because YOU didn’t implement a good business system. Blaming people will often prevent you from uncovering the true source of the problem.
Take a look around your business today. Can you improve the layout, working conditions, or get more organized? Can you reduce rework, downtime, distractions, and complexity? Can you get those half-finished jobs completed? For increased profit, find ways now to reduce and simplify your business operations.